Le HT PEK fait partie de la famille des polymères semi-cristallins polyéthercétones, qui comprend également le PEEK et le PAEK. Développé par Victrex, l’un des principaux producteurs de PEEK, il présente des avantages en termes de performances par rapport à ces autres matériaux polycétoniques semi-cristallins sur plusieurs fronts.
Une amélioration des performances du PEEK
Développé par Victrex et disponible dans le commerce sous le nom de Victrex HT PEK, l’un de ses principaux avantages est sa température de transition vitreuse (Tg) de 160°C (320°F), soit 10°C (18°F) de plus que celle du PEEK. Bien que comparable à température ambiante, le PEK HT conserve une plus grande résistance à température élevée. Par exemple, le PEK HT présente un module de fluage plus de deux fois supérieur à celui du PEEK non renforcé à 150°C (302°F) – la Tg du PEEK.
Ses performances dans les applications de support de charge dynamique sont également excellentes. Les essais réalisés par Victrex ont montré que la résistance à l’usure du PEK HT était plus de trois fois supérieure à celle du PEEK standard non chargé de Victrex. Pour les applications nécessitant une résistance à la rupture par fatigue à des niveaux de contrainte élevés, le HT PEK est également plus performant que le PEEK.
Comme tous les polyéthercétones, le HT PEK résiste à une exposition à long terme à un large éventail de produits chimiques. Le PEEK est cependant imperméable à la plus large gamme de produits chimiques parmi les membres de la famille des polyéthercétones, en raison du rapport éther (E)/cétone (K) de sa structure polymérique.
PEK HT non rempli et renforcé
Le grade standard de Victrex pour le moulage par injection non renforcé est désigné HT G22 PEK. Bien que sa résistance soit excellente à haute température, Drake Plastics moule également par injection un grade renforcé de 30 % de fibres de verre pour les composants qui nécessitent une plus grande rigidité structurelle.
Applications typiques du HT PEK
Les propriétés du PEK HT en font un candidat solide pour les applications qui nécessitent une augmentation des performances par rapport au PEEK standard. Les applications potentielles des composants HT PEK moulés par injection sont les suivantes :
- Joints d’étanchéité, sièges de soupape, isolateurs électriques dans les équipements pétroliers et gaziers de fond de puits.
- Joints de cloison à paroi mince, connecteurs dans les pompes électriques submersibles (ESP).
- Composants de l’échangeur de chaleur
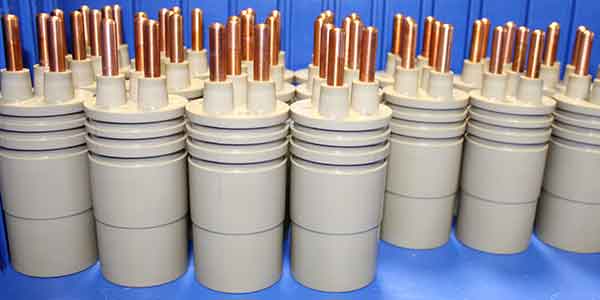
Les capacités de Drake Plastics pour mouler par injection le PEK HT
Drake Plastics propose des dimensions de machines polyvalentes pour mouler par injection une large gamme de configurations de pièces HT PEK. Nos machines de moulage ont une capacité de 35 à 300 tonnes et produisent des composants de précision allant de 0,85 gramme (0,03 oz) à 567 grammes (20 oz).
Les conditions de moulage par injection pour le PEK HT comprennent des températures de fusion extrêmement élevées et une fenêtre de traitement étroite. Drake Plastics utilise une technologie de traitement spécialement conçue pour ces types de polymères. La combinaison de notre expérience en matière de traitement des matières fondues et de notre technologie de moulage par injection nous permet de produire des pièces de haute qualité à partir de HT PEK et d’autres polycétones.
Analyse de l'écoulement de la matière fondue :
Les ingénieurs de Drake Plastics utilisent l’analyse de l’écoulement de la matière fondue pour caractériser le PEK HT et d’autres polymères avancés avant leur transformation. L’approche analytique permet de définir les meilleurs paramètres de traitement, la configuration de l’équipement de moulage et la conception de l’outillage pour chaque polymère et chaque configuration de pièce que nous produisons.
La technologie permet d'obtenir une qualité et des performances constantes :
Les machines de moulage par injection entièrement électriques de Drake Plastics fonctionnent de manière constante, efficace et propre, sans risque de fuite de fluide hydraulique.
Nos ingénieurs dimensionnent les fûts en fonction de chaque polymère. Cela minimise le temps pendant lequel un thermoplastique reste à sa température de fusion, évitant ainsi la dégradation du matériau et garantissant que les propriétés optimales du matériau sont préservées dans chaque composant que nous moulons.
Nous concevons également nos systèmes de contrôle spécifiquement pour le traitement des polymères à haute performance. Pendant le moulage, des sondes sont placées dans chaque cavité du moule pour surveiller les températures et les pressions, et maintenir les conditions qui optimisent la qualité et les performances de chaque composant PEK HT que nous produisons.
L’équipement de moulage de Drake Plastics est doté d’une capacité supplémentaire : la technologie de compression par injection. Il nous permet de comprimer ou de « coincer » les pièces à l’intérieur du moule pendant qu’elles refroidissent. La séquence de post-injection élimine les porosités et les vides qui peuvent se produire notamment avec les pièces moulées à parois lourdes.
Victrex ST PEKEKK : Une option pour les applications à haute température
La famille des polymères polycétones comprend une alternative encore plus performante au HT PEK pour les applications plus exigeantes. Désigné Victrex ST PEKEKK, Drake Plastics moule par injection ce polymère pour des applications où son avantage de 10°C (18°F) en termes de température de transition du verre par rapport au PEK HT peut s’avérer bénéfique.
Semi-produits pour prototypes usinés en PEK HT
Drake Plastics propose des barres rondes et des plaques extrudées non renforcées en Victrex HT G45 PEK, en stock et en dimensions personnalisées. Des formes usinables en HT PEK renforcé ainsi qu’en Victrex ST sont également disponibles sur commande avec des minimums raisonnables. Les clients ont ainsi la possibilité de faire usiner des prototypes pour les tester, ou des quantités de production avant de finaliser les outils de moulage par injection. Drake Plastics propose également des services d’usinage CNC et fournit à d’autres sociétés d’usinage une assistance technique pour produire des composants usinés de la plus haute qualité possible à partir de nos formes en stock.
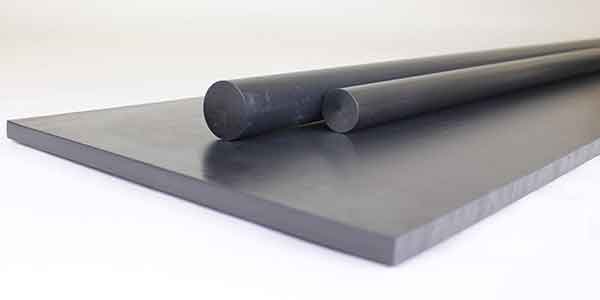